Natural Gas
Sapphire Technologies designs, develops and manufactures highly engineered FreeSpin® In-line Turboexpanders (FIT) for natural gas processing and distribution systems. The FIT extracts energy from the pressure reduction required at various stages of gas distribution and allows for the generation of electricity with no added pollution.
Sapphire’s FreeSpin® turboexpander is an innovative and economically viable solution to increase the energy efficiency of a natural gas processing plant or distribution facility. The turboexpander is designed to operate at gas inlet pressures up to 1,600 psig. The 300 kW FIT enables Sapphire’s customers to scale up their power generation capacity by installing multiple units in parallel with the regulating valves.
Natural Gas Pressure Letdown Application and Turboexpander
Natural gas is pressurized to facilitate transportation across long distances through pipelines. The pressure is stepped down at pressure letdown (PLD) stations (city gates) at various stages throughout the network. The PLD station depressurizes the gas to lower levels for safe delivery to industrial, commercial and residential end users. The PLD stations use regulating valves to achieve the required pressure drop but also waste significant energy in the process. A turboexpander generator, such as FIT, can be installed in parallel to the regulating valve in order to recover the wasted energy from the pressure reduction and produce electricity.
How Application Works
- The pre-heated high-pressure gas flows into the FreeSpin® In-line Turboexpander.
- The gas then expands through the radial turbine wheel.
- The low-pressure gas exits the turboexpander and is ready for delivery to residential and commercial users.
- The energy wasted during the pressure reduction process is recovered by the FIT and converted to electrical power.
- Any excess high-pressure gas not directed through the turboexpander is expanded by the conventional pressure regulator, which is installed in parallel to the FIT.
- The produced electricity enters the power electronics unit, which can be programmed to specific power requirement
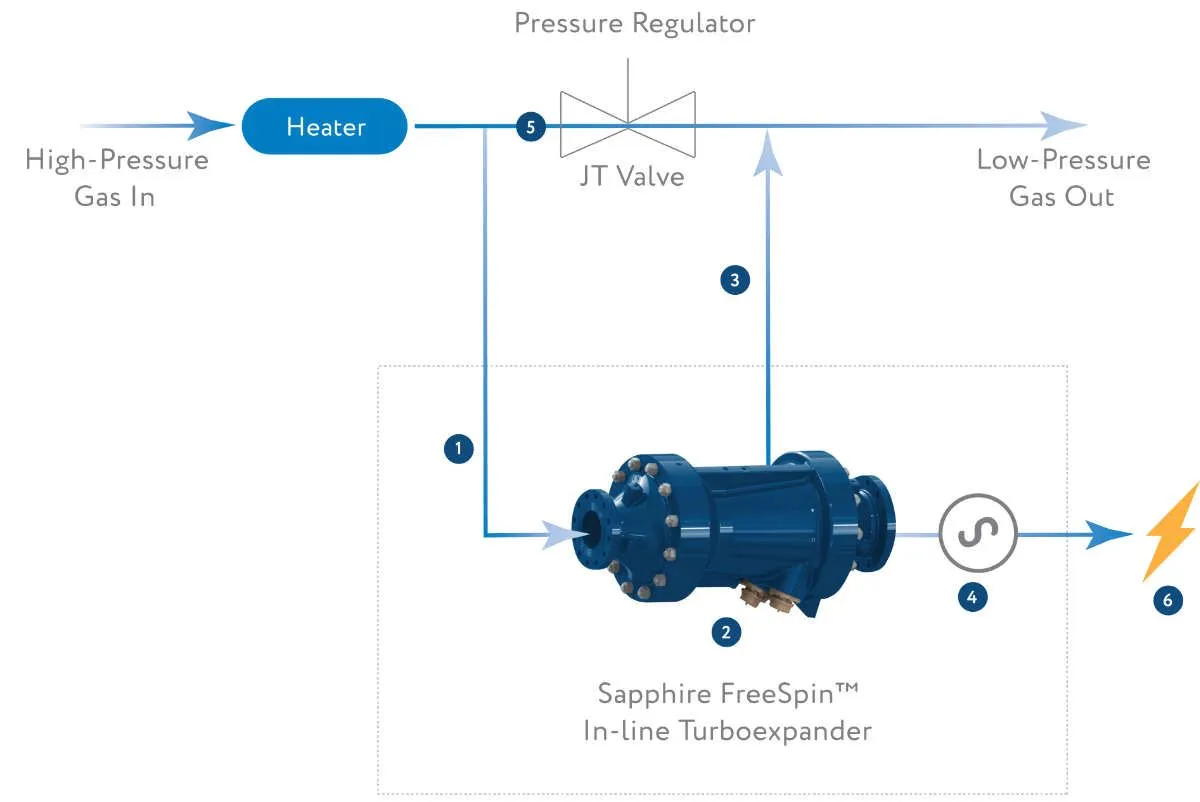
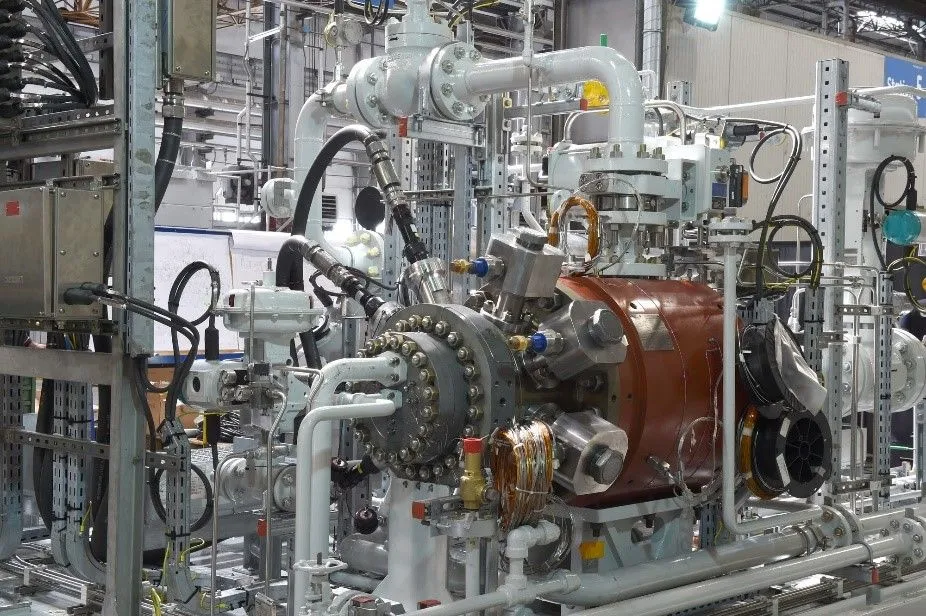
Case Study
Baker Hughes, one of the world's largest oilfield services companies, selected Sapphire’s parent company, Calnetix Technologies, to provide design and manufacturing services for a turboexpander generator to be utilized at a natural gas PLD station. The turboexpander, coupled to a high-speed generator, would allow kinetic energy to be converted into electrical energy in natural gas pipelines while still reducing the gas pressure.
The turboexpander generator co-developed, tested and commissioned by the customer in conjunction with Sapphire’s parent company, Calnetix, consists of a 300 kW radial inflow turbine equipped with a fully integrated and sealed high-speed generator. Calnetix was responsible for designing and building the permanent magnet (PM) synchronous generator supported by PM-biased homopolar active magnetic bearings (AMBs). The rated speed of the generator is 30,000 RPM, the maximum continuous speed is 31,500 RPM and the overspeed limit of the generator is 36,300 RPM. The PLD expander generator was also provided with a Variable Speed Drive (VSD) and a Magnetic Bearing Controller (MBC). A touchdown bearing system was implemented using rolling element bearings with soft mount supports.
While developing the turboexpander generator machine, one of the main challenges was to keep an approximate distance of 100 feet between the machine and the controller due to the potentially explosive nature of the environment, thus making it a long cable application. Another challenge was the backup bearings selected for this application consist of two separate rows of balls, contained by two separate outer rings and a single inner ring construction. A series of drop tests were performed on the PLD expander to test the reliability of the backup bearings. During the drop testing, it was observed that the inner ring was heating up on acceleration, thereby increasing the load on the balls and moving them in the axial direction. A retainer spring was used to provide external axial load to keep the bearing in place.
Compared to conventional expanders, the 300 kW AMB-supported turboexpander generator provided the following advantages:
- High system efficiency
- Operational life of 40,000 hours without maintenance
- Lubrication-free system
The turboexpander generator was commissioned at the customer site in April of 2019 and has been operating in parallel with a Joule-Thomson valve. The PLD turboexpander is producing 1,600,000 kWh per year. It is expected that several additional units will be commissioned in next 24 months at the customer’s sites.
Latest News & Upcoming Events
Additional Resources
Technical Papers
Product Brochures & Media
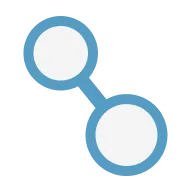
Hydrogen Gas
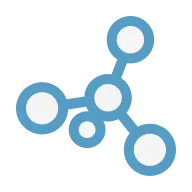